Your cart is currently empty!
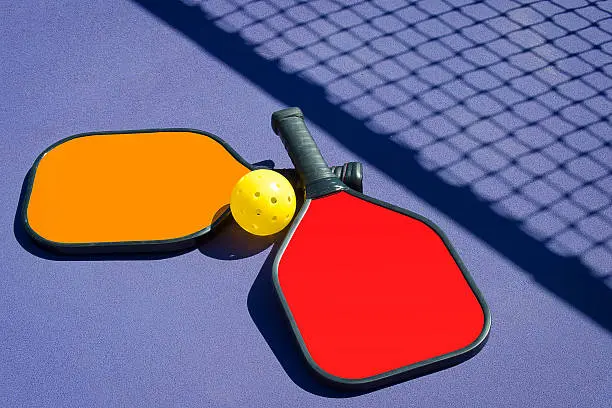
How Fiberglass Pickleball Paddles Are Made 2025?
[et_pb_section fb_built=”1″ _builder_version=”4.27.4″ _module_preset=”default” background_color=”rgba(131,0,233,0.15)” global_colors_info=”{}”][et_pb_row _builder_version=”4.27.4″ _module_preset=”default” min_height=”92.8px” global_colors_info=”{}”][et_pb_column type=”4_4″ _builder_version=”4.27.4″ _module_preset=”default” global_colors_info=”{}”][et_pb_text _builder_version=”4.27.4″ _module_preset=”default” global_colors_info=”{}”]
Pickleball has become one of the fastest-growing sports globally, bringing with it a surge in demand for high-quality paddles. Among the various materials used to craft these paddles, fiberglass stands out for its unique blend of affordability, performance, and durability. But have you ever wondered how fiberglass pickleball paddles are made? In this behind-the-scenes guide, we’ll take you through the entire manufacturing process, from raw materials to the final product.
[/et_pb_text][et_pb_text _builder_version=”4.27.4″ _module_preset=”default” text_font=”|700|||||||” text_text_color=”#000000″ text_font_size=”17px” background_color=”#E09900″ global_colors_info=”{}”]
Key takeaways: how are fiberglass pickleball paddles produced? cold pressed pickleball paddle
[/et_pb_text][et_pb_image src=”https://lixipickleball.com/wp-content/uploads/2024/12/fiberglass-pickleball-paddle-production.webp” alt=”fiberglass pickleball paddle production” title_text=”fiberglass pickleball paddle production” _builder_version=”4.27.4″ _module_preset=”default” global_colors_info=”{}”][/et_pb_image][/et_pb_column][/et_pb_row][/et_pb_section][et_pb_section fb_built=”1″ _builder_version=”4.27.4″ _module_preset=”default” background_color=”rgba(124,218,36,0.2)” global_colors_info=”{}”][et_pb_row _builder_version=”4.27.4″ _module_preset=”default” min_height=”158.5px” global_colors_info=”{}”][et_pb_column type=”4_4″ _builder_version=”4.27.4″ _module_preset=”default” global_colors_info=”{}”][et_pb_heading title=”What Makes Fiberglass Special in Pickleball Paddles?” _builder_version=”4.27.4″ _module_preset=”default” title_level=”h2″ title_font=”|700|||||||” global_colors_info=”{}”][/et_pb_heading][et_pb_text _builder_version=”4.27.4″ _module_preset=”default” global_colors_info=”{}”]
Fiberglass is a lightweight and versatile material known for its ability to provide excellent control and a softer touch. These qualities make fiberglass paddles a popular choice among beginners and intermediate players. Here’s why:
- Enhanced Control: Fiberglass surfaces flex slightly upon contact, allowing for better placement and spin.
- Affordability: Compared to carbon fiber paddles, fiberglass options are generally more budget-friendly.
- Durability: With proper care, fiberglass paddles can withstand regular play without compromising performance.
- Vibrant Aesthetic: Fiberglass surfaces are easy to customize with colorful designs.
[/et_pb_text][et_pb_image src=”https://lixipickleball.com/wp-content/uploads/2024/12/fiberglass-pickleball-paddle.webp” alt=”fiberglass pickleball paddles” title_text=”fiberglass pickleball paddle” _builder_version=”4.27.4″ _module_preset=”default” global_colors_info=”{}”][/et_pb_image][/et_pb_column][/et_pb_row][/et_pb_section][et_pb_section fb_built=”1″ _builder_version=”4.27.4″ _module_preset=”default” background_color=”rgba(237,240,0,0.16)” global_colors_info=”{}”][et_pb_row _builder_version=”4.27.4″ _module_preset=”default” custom_padding=”||39px|||” global_colors_info=”{}”][et_pb_column type=”4_4″ _builder_version=”4.27.4″ _module_preset=”default” global_colors_info=”{}”][et_pb_heading title=”Step 1: Sourcing the Raw Materials” _builder_version=”4.27.4″ _module_preset=”default” title_level=”h2″ title_font=”|700|||||||” global_colors_info=”{}”][/et_pb_heading][et_pb_text _builder_version=”4.27.4″ _module_preset=”default” global_colors_info=”{}”]
The manufacturing process begins with sourcing high-quality materials. Each component of the paddle plays a crucial role in determining its performance.
1. Fiberglass Sheets
- What Are They?
Fiberglass is composed of thin glass fibers woven into a fabric-like material. These sheets are lightweight, flexible, and strong. - Quality Control: Manufacturers select fiberglass sheets with consistent thickness and strength to ensure uniform performance across paddles.
2. Core Materials
The paddle’s core provides structure and determines its weight and responsiveness. Common core materials include:
- Polypropylene Honeycomb: Lightweight and offers excellent shock absorption.
- Nomex Honeycomb: Stiffer and provides more power, preferred by competitive players.
- Aluminum Core: Durable and heavier, ideal for players seeking control.
3. Handles and Grips
The handle is typically made of a lightweight material like foam or wood, while grips are crafted from PU (polyurethane) for comfort and sweat resistance.
[/et_pb_text][/et_pb_column][/et_pb_row][/et_pb_section][et_pb_section fb_built=”1″ _builder_version=”4.27.4″ _module_preset=”default” background_color=”rgba(224,153,0,0.23)” global_colors_info=”{}”][et_pb_row _builder_version=”4.27.4″ _module_preset=”default” min_height=”162.5px” global_colors_info=”{}”][et_pb_column type=”4_4″ _builder_version=”4.27.4″ _module_preset=”default” global_colors_info=”{}”][et_pb_heading title=”Step 2: Designing the Paddle” _builder_version=”4.27.4″ _module_preset=”default” title_level=”h2″ title_font=”|700|||||||” global_colors_info=”{}”][/et_pb_heading][et_pb_text _builder_version=”4.27.4″ _module_preset=”default” global_colors_info=”{}”]
Before production begins, the paddle’s design is finalized. This includes its dimensions, weight distribution, and aesthetic features.
1. Determining Paddle Specifications
Manufacturers follow industry standards for paddle dimensions, ensuring compliance with USA Pickleball regulations:
- Maximum Size: 24 inches in total (length + width).
- Thickness: Often around 16mm for optimal performance.
2. Customization Options
- Surface Texture: A slightly roughened surface enhances spin potential.
- Graphics: Fiberglass paddles are easy to print on, allowing for vibrant custom designs.
- Edge Guards: Protect the paddle from impacts and improve durability.
[/et_pb_text][/et_pb_column][/et_pb_row][/et_pb_section][et_pb_section fb_built=”1″ _builder_version=”4.27.4″ _module_preset=”default” background_color=”rgba(124,218,36,0.2)” global_colors_info=”{}”][et_pb_row _builder_version=”4.27.4″ _module_preset=”default” min_height=”158.5px” global_colors_info=”{}”][et_pb_column type=”4_4″ _builder_version=”4.27.4″ _module_preset=”default” global_colors_info=”{}”][et_pb_heading title=”Step 3: Laminating the Fiberglass Surface” _builder_version=”4.27.4″ _module_preset=”default” title_level=”h2″ title_font=”|700|||||||” global_colors_info=”{}”][/et_pb_heading][et_pb_text _builder_version=”4.27.4″ _module_preset=”default” global_colors_info=”{}”]
The fiberglass surface is laminated onto the core, creating the paddle’s striking face.
1. Adhesive Application
- A specialized adhesive is applied to the core and fiberglass sheet. This glue must bond securely while maintaining the paddle’s lightweight properties.
2. Fiberglass Layering
- The fiberglass sheets are carefully positioned on both sides of the core. Some paddles feature multiple fiberglass layers for added durability and performance.
3. Heat and Pressure
- The paddle is placed in a heat press, where high temperatures and pressure fuse the fiberglass and core materials. This step is crucial for ensuring a smooth, even surface.
[/et_pb_text][/et_pb_column][/et_pb_row][/et_pb_section][et_pb_section fb_built=”1″ _builder_version=”4.27.4″ _module_preset=”default” background_color=”rgba(224,43,32,0.22)” global_colors_info=”{}”][et_pb_row _builder_version=”4.27.4″ _module_preset=”default” custom_padding=”||38px|||” global_colors_info=”{}”][et_pb_column type=”4_4″ _builder_version=”4.27.4″ _module_preset=”default” global_colors_info=”{}”][et_pb_heading title=”Step 4: Cutting and Shaping the Core” _builder_version=”4.27.4″ _module_preset=”default” title_level=”h2″ title_font=”|700|||||||” global_colors_info=”{}”][/et_pb_heading][et_pb_text _builder_version=”4.27.4″ _module_preset=”default” global_colors_info=”{}”]
Once the materials are sourced, the production process begins with the paddle core.
1. Cutting the Core Material
- Precision Cutting: The honeycomb core material is cut into the desired paddle shape using CNC (computer numerical control) machines. Precision ensures consistent performance.
- Thickness Adjustment: Manufacturers may shave the core to achieve the desired thickness, balancing power and control.
2. Forming the Handle Slot
A slot is cut into the core to attach the handle securely. This ensures the paddle maintains its structural integrity during intense play.
[/et_pb_text][/et_pb_column][/et_pb_row][/et_pb_section][et_pb_section fb_built=”1″ _builder_version=”4.27.4″ _module_preset=”default” background_color=”rgba(237,240,0,0.16)” global_colors_info=”{}”][et_pb_row _builder_version=”4.27.4″ _module_preset=”default” custom_padding=”||39px|||” global_colors_info=”{}”][et_pb_column type=”4_4″ _builder_version=”4.27.4″ _module_preset=”default” global_colors_info=”{}”][et_pb_heading title=”Step 5: Shaping and Trimming” _builder_version=”4.27.4″ _module_preset=”default” title_level=”h2″ title_font=”|700|||||||” global_colors_info=”{}”][/et_pb_heading][et_pb_text _builder_version=”4.27.4″ _module_preset=”default” global_colors_info=”{}”]
After lamination, the paddle takes shape, but some finishing touches are required.
1. Trimming the Edges
- Excess fiberglass and adhesive are trimmed off using precision tools to create clean, smooth edges.
2. Adding the Edge Guard
- Edge guards are affixed to the paddle’s perimeter to protect it from impacts and extend its lifespan. These guards are often made of lightweight plastic or rubber.
[/et_pb_text][/et_pb_column][/et_pb_row][/et_pb_section][et_pb_section fb_built=”1″ _builder_version=”4.27.4″ _module_preset=”default” background_color=”rgba(224,153,0,0.23)” global_colors_info=”{}”][et_pb_row _builder_version=”4.27.4″ _module_preset=”default” min_height=”162.5px” global_colors_info=”{}”][et_pb_column type=”4_4″ _builder_version=”4.27.4″ _module_preset=”default” global_colors_info=”{}”][et_pb_heading title=”Step 6: Assembling the Handle” _builder_version=”4.27.4″ _module_preset=”default” title_level=”h2″ title_font=”|700|||||||” global_colors_info=”{}”][/et_pb_heading][et_pb_text _builder_version=”4.27.4″ _module_preset=”default” global_colors_info=”{}”]
The handle is where players interact most with the paddle, making its construction critical.
1. Attaching the Handle
- The handle is inserted into the pre-cut slot in the core and secured with industrial-grade adhesives.
- Some manufacturers reinforce the handle with screws or additional adhesives to prevent loosening.
2. Wrapping the Grip
- A polyurethane grip is wrapped around the handle for comfort and control. Many grips feature sweat-wicking properties and perforations for improved ventilation.
[/et_pb_text][/et_pb_column][/et_pb_row][/et_pb_section][et_pb_section fb_built=”1″ _builder_version=”4.27.4″ _module_preset=”default” background_color=”rgba(124,218,36,0.2)” global_colors_info=”{}”][et_pb_row _builder_version=”4.27.4″ _module_preset=”default” min_height=”158.5px” global_colors_info=”{}”][et_pb_column type=”4_4″ _builder_version=”4.27.4″ _module_preset=”default” global_colors_info=”{}”][et_pb_heading title=”Step 7: Quality Control” _builder_version=”4.27.4″ _module_preset=”default” title_level=”h2″ title_font=”|700|||||||” global_colors_info=”{}”][/et_pb_heading][et_pb_text _builder_version=”4.27.4″ _module_preset=”default” global_colors_info=”{}”]
Each paddle undergoes rigorous quality checks to ensure it meets performance and durability standards.
1. Surface Inspection
- The paddle surface is inspected for smoothness, uniformity, and proper adhesion.
2. Weight and Balance Testing
- Paddles are weighed to ensure they fall within the specified range (usually 7-8 ounces).
- The balance is tested to confirm even weight distribution.
3. Playtesting
- Random paddles from each batch are playtested by skilled players to evaluate performance, including control, power, and spin.
[/et_pb_text][/et_pb_column][/et_pb_row][/et_pb_section][et_pb_section fb_built=”1″ _builder_version=”4.27.4″ _module_preset=”default” background_color=”rgba(224,43,32,0.22)” global_colors_info=”{}”][et_pb_row _builder_version=”4.27.4″ _module_preset=”default” custom_padding=”||38px|||” global_colors_info=”{}”][et_pb_column type=”4_4″ _builder_version=”4.27.4″ _module_preset=”default” global_colors_info=”{}”][et_pb_heading title=”Step 8: Customization and Branding” _builder_version=”4.27.4″ _module_preset=”default” title_level=”h2″ title_font=”|700|||||||” global_colors_info=”{}”][/et_pb_heading][et_pb_text _builder_version=”4.27.4″ _module_preset=”default” global_colors_info=”{}”]
For customizable paddles, this step involves adding the buyer’s unique branding or graphics.
1. UV Printing
- Advanced UV printing technology is used to apply logos, patterns, and colors directly onto the fiberglass surface. This method ensures vibrant, long-lasting designs.
2. Packaging
- Finished paddles are packaged in branded boxes with protective layers to prevent damage during transit.
[/et_pb_text][/et_pb_column][/et_pb_row][/et_pb_section][et_pb_section fb_built=”1″ _builder_version=”4.27.4″ _module_preset=”default” background_color=”rgba(237,240,0,0.16)” global_colors_info=”{}”][et_pb_row _builder_version=”4.27.4″ _module_preset=”default” custom_padding=”||39px|||” global_colors_info=”{}”][et_pb_column type=”4_4″ _builder_version=”4.27.4″ _module_preset=”default” global_colors_info=”{}”][et_pb_heading title=”The Future of Fiberglass Pickleball Paddles” _builder_version=”4.27.4″ _module_preset=”default” title_level=”h2″ title_font=”|700|||||||” global_colors_info=”{}”][/et_pb_heading][et_pb_text _builder_version=”4.27.4″ _module_preset=”default” global_colors_info=”{}”]
As pickleball continues to grow in popularity, manufacturers are innovating to improve the performance and sustainability of fiberglass paddles. Future trends include:
- Eco-Friendly Materials: Exploring biodegradable cores and recyclable fiberglass alternatives.
- Enhanced Spin Technology: Developing textured fiberglass surfaces for even greater spin potential.
- Smart Paddles: Integrating sensors to track metrics like swing speed and impact points.
[/et_pb_text][et_pb_image src=”https://lixipickleball.com/wp-content/uploads/2024/12/how-is-fiberglass-pickleball-paddle-made.webp” alt=”how is fiberglass pickleball paddle made” title_text=”how is fiberglass pickleball paddle made” _builder_version=”4.27.4″ _module_preset=”default” global_colors_info=”{}”][/et_pb_image][/et_pb_column][/et_pb_row][/et_pb_section][et_pb_section fb_built=”1″ _builder_version=”4.27.4″ _module_preset=”default” background_color=”rgba(31,221,202,0.18)” global_colors_info=”{}”][et_pb_row _builder_version=”4.27.4″ _module_preset=”default” custom_padding=”||37px|||” global_colors_info=”{}”][et_pb_column type=”4_4″ _builder_version=”4.27.4″ _module_preset=”default” global_colors_info=”{}”][et_pb_heading title=”Conclusion” _builder_version=”4.27.4″ _module_preset=”default” title_level=”h2″ title_font=”|700|||||||” global_colors_info=”{}”][/et_pb_heading][et_pb_text _builder_version=”4.27.4″ _module_preset=”default” global_colors_info=”{}”]
The process of creating fiberglass pickleball paddles is a blend of art and engineering. Here’s a quick recap of the key steps:
- Raw Material Sourcing: Fiberglass sheets, honeycomb cores, and ergonomic handles form the foundation.
- Designing: Specifications like size, weight, and graphics are determined.
- Core Preparation: The honeycomb core is cut and shaped with precision.
- Lamination: Fiberglass surfaces are adhered to the core using heat and pressure.
- Shaping and Trimming: Excess materials are removed, and edge guards are added.
- Handle Assembly: Handles are secured and wrapped for player comfort.
- Quality Control: Every paddle undergoes rigorous testing to ensure top-notch performance.
- Customization: Logos, graphics, and packaging complete the paddle.
Fiberglass paddles are a cornerstone of the pickleball world, offering players a perfect balance of control, durability, and cost-efficiency. By understanding the craftsmanship behind these paddles, players can appreciate their equipment even more.
[/et_pb_text][et_pb_text _builder_version=”4.27.4″ _module_preset=”default” global_colors_info=”{}”]
More pickleball paddle resource:
[/et_pb_text][/et_pb_column][/et_pb_row][/et_pb_section][et_pb_section fb_built=”1″ _builder_version=”4.27.4″ _module_preset=”default” background_color=”rgba(178,164,10,0.18)” global_colors_info=”{}”][et_pb_row _builder_version=”4.27.4″ _module_preset=”default” custom_padding=”||37px|||” global_colors_info=”{}”][et_pb_column type=”4_4″ _builder_version=”4.27.4″ _module_preset=”default” global_colors_info=”{}”][et_pb_heading title=”FAQ” _builder_version=”4.27.4″ _module_preset=”default” title_level=”h2″ title_font=”|700|||||||” global_colors_info=”{}”][/et_pb_heading][et_pb_text _builder_version=”4.27.4″ _module_preset=”default” global_colors_info=”{}”]
Q1: What are the benefits of fiberglass pickleball paddles?
Fiberglass paddles offer excellent control, a softer touch, and are budget-friendly compared to carbon fiber alternatives. They’re ideal for beginners and intermediate players.
Q2: How does fiberglass compare to carbon fiber in pickleball paddles?
Fiberglass provides more control and a softer feel, while carbon fiber delivers more power and durability. The choice depends on your playing style.
Q3: Are fiberglass pickleball paddles durable?
Yes, fiberglass paddles are durable and can withstand regular play. However, they may not be as long-lasting as carbon fiber paddles under heavy usage.
Q4: Can fiberglass paddles be customized?
Absolutely! Fiberglass paddles are ideal for customization, offering vibrant graphics and personalized branding options.
Q5: How should I maintain my fiberglass paddle?
Clean the surface with a damp cloth after each use, avoid exposing it to extreme temperatures, and store it in a protective cover to extend its lifespan.
[/et_pb_text][et_pb_text _builder_version=”4.27.4″ _module_preset=”default” background_color=”#7CDA24″ global_colors_info=”{}”]
We are manufacturer of custom branding pickleball paddle,padel rackets and beach tennis, contact us to discuss custom solutions for your brand!
[/et_pb_text][/et_pb_column][/et_pb_row][/et_pb_section]
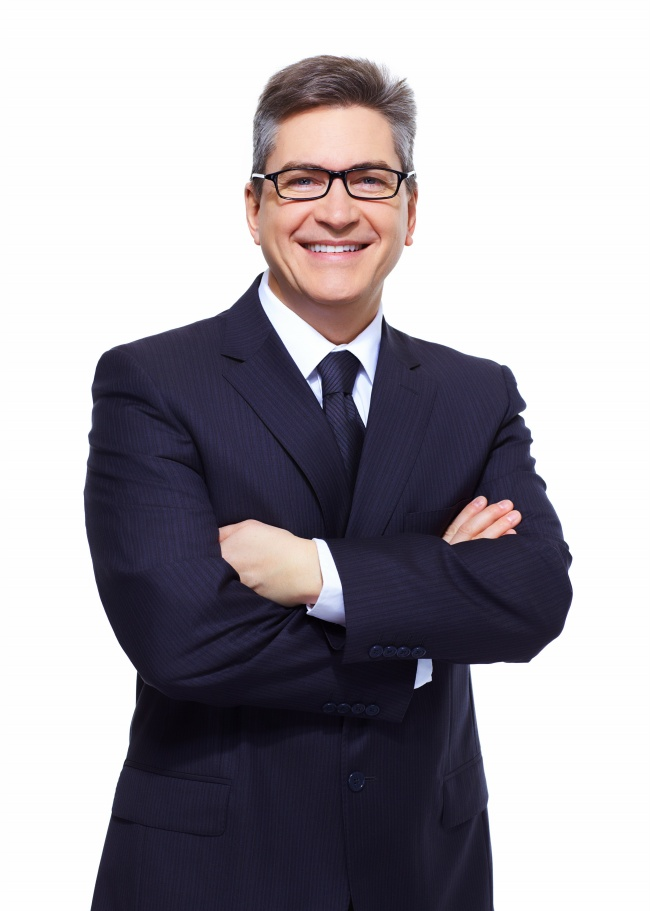
I am Edward lee, founder of lixisports, with 10 years experience in manufacturing
How can I provide custom solutions to boost your business?
Comments
One response to “How Fiberglass Pickleball Paddles Are Made 2025?”
[…] How Fiberglass Pickleball Paddles Are Made 2025? […]
Leave a Reply